Современное дорожное строительство является одной из самых материалоемких отраслей народного хозяйства, требующих значительных капиталовложений. В этих условиях контроль качества материалов как при их производстве, так и применении стал обязательным компонентом в дорожном строительстве. При этом необходимо учитывать, что в настоящее время не только быстро расширяется номенклатура используемых материалов, но и увеличивается перечень показателей, требующих контроля. Для обеспечения выполнения указанных требований необходимы не только новые технологии, но и средства как лабораторного, так и оперативного полевого контроля используемых материалов и компонентов, а также физико-механических и геометрических показателей получаемых при этом покрытий.
В настоящее время Группа компаний «Современные дорожные технологии» выпускает большую номенклатуру современных приборов и средств контроля, которые могут применяться не только дорожными лабораториями и строительными организациями, но также использоваться в составе передвижных дорожных лабораторий. Номенклатура включает в себя приборы и оборудование для диагностики и контроля при строительстве автодорог, лабораторные приборы для испытания асфальтобетона и его компонентов, цементобетона, грунтов, а также контроля качества шероховатой поверхностной обработки и лакокрасочных материалов, используемых в дорожном строительстве.
Помимо традиционного оборудования, использующего известные механические и геометрические способы измерений, таких как рейка дорожная, устройство контроля геометрических параметров автомобильных дорог, измеритель колейности, динамический плотномер, прогибомер длиннобазовый, баллонный плотномер, пенетрометр и многие другие, предприятие успешно осваивает выпуск автоматизированного оборудования, включающего в себя электронные, электромеханические и программные компоненты. Некоторые из них объединены в комплекты оборудования, позволяющие решать задачи целого направления в исследовании новых свойств дорожных материалов.
В настоящее время в РФ на смену проектирования асфальтобетона по физическим показателям (по ГОСТ 12801) приходят методы объемного проектирования по эксплуатационным характеристикам: по Маршаллу и Суперпейв (ГОСТ 58401, ГОСТ 58406).
Метод Маршалла основан на проектировании состава асфальтобетонной смеси, уплотненной с помощью ударного компактора и испытанной по 4 показателям: плотность, остаточная пористость, устойчивость и условная пластичность.
С 2019 года на нашем предприятии выпускается набор приборов для испытаний по методу Маршалла: уплотнитель Маршалла (ударный компактор), вакуумный пикнометр, приспособление обжимное для испытания образцов по методу Маршалла (ГОСТ Р 58406.8-2019), приспособление для определения предела прочности при непрямом растяжении (ГОСТ Р 58401.18-2019), приспособление опорное для испытания образцов на изгиб (ГОСТ Р 58406.6-2020).
Ударный компактор предназначен для подготовки цилиндрических образцов диаметром (101,6±0,1) мм и высотой (63,5±2,5) мм, а также образцов диаметром (152,4±0,2) мм и высотой (95,2±2,5) мм из асфальтобетонной дорожной смеси и асфальтобетона, предназначенных для устройства конструктивных слоёв дорожной одежды на автомобильных дорогах по ГОСТ Р 58406.9-2019. Образец формируется в специальной форме под ударами падающего груза. Установка автоматически уплотняет образец, совершая 50 ударов в минуту, и останавливается после того, как заданное количество ударов завершено.
Принцип работы вакуумного пикнометра основан на определении плотности размельчённой пробы асфальтобетонной смеси после удаления воздушных пустот. Удаление воздушных пустот достигается путём вакуумирования пробы асфальтобетонной смеси в совокупности с применением лёгкой вибрации. Установка предназначена для получения в рабочей камере вакуума определенной величины, необходимого для определения показателей:
- максимальной плотности асфальтобетонной смеси;
- содержания воздушных пустот в асфальтобетоне;
- пустот наполненных битумным вяжущим;
- истинной плотности асфальтобетонной смеси по ГОСТ 12801-98;
- водонасыщения по ГОСТ 12801-98.
Другим примером комплексного подхода к решению одновременно нескольких задач в составе одного комплекта является малогабаритный гидравлический пресс ПГИ-500, выпускаемый предприятием с 2003 года. Пресс, развивающий усилия до 500 кН (50 тонн), первоначально предназначался для испытания на сжатие образцов асфальтобетона и других строительных материалов при скорости деформирования не более 4 мм/мин.
Последовательное совершенствование конструкции, гидравлической схемы и программного обеспечения пресса позволило увеличить скорость первоначально до 10 мм/мин, а в последствии, и до 150 мм/мин. Это обеспечило возможность формования образцов асфальтобетона в соответствии с требованиями ГОСТ 12801-98 «Материалы на основе органических вяжущих для дорожного и аэродромного строительства. Методы испытаний».
В результате модернизации, проведенной в последнее время, значительно расширены технологические и эксплуатационные возможности пресса. Номенклатура производимых на прессе операций дополнена целым комплексом испытаний, предусмотренных ГОСТ 12801-98, и проводимых при скорости движения подъемной плиты 50 мм/мин:
определение характеристик сдвигоустойчивости при сжатии специальным обжимным устройством по схеме Маршалла;
определение характеристик сдвигоустойчивости при одноосном сжатии;
определение предела прочности на растяжение при расколе.
Пресс позволяет проводить не только испытания образцов, но и приготовление асфальтобетонных образцов прессованием. Для достижения требуемой по ГОСТ 12801 скорости нарастания нагрузки пресс обеспечивает соответствующую высокую скорость перемещения подъемной плиты — до 150 мм/мин. Это требование зачастую не выполняется другими аналогичными малогабаритными испытательными машинами.
Величина хода подъемной плиты увеличена с прежних 45 до 70 мм, что расширяет возможности пресса при проведении испытаний щебня на дробимость с использованием любых, в том числе и низкопрочных марок материалов.
Для отсчета величины перемещений и деформаций образцов в новой конструкции использован бесконтактный лазерный датчик, что повышает надежность работы пресса и точность полученных результатов испытаний.
Пресс может комплектоваться устройством для извлечения асфальтобетонных образцов из форм по ГОСТ 12801. Устройство работает от насосной станции пресса и легко встраивается в его гидравлическую систему.
Пульт управления пресса может быть подключен к персональному компьютеру, что позволяет производить обработку и хранение результатов испытаний, представлять их в любой удобной форме (в виде таблиц, графиков и т. д.), производить расчет ряда параметров и ведение базы результатов испытаний с возможностью их последующего документирования.
По желанию заказчика пресс может комплектоваться соответствующими приспособлениями.
Таким образом, в настоящее время пресс ПГИ-500-02 — это сертифицированное средство измерения утвержденного типа, которое можно считать универсальным испытательным комплектом оборудования, обеспечивающим весь технологический цикл лабораторных работ по испытанию образцов асфальтобетонных материалов начиная от их приготовления, извлечения из форм и весь комплекс испытаний в автоматических режимах при сжатии в полном объеме требований ГОСТ 12801-98.
Аналогичный пресс, но усилием уже до 1000 кН (100 тонн) предназначен, в основном, для испытания цементобетонов и других строительных материалов.
В современных условиях транспортная нагрузка на полотно автомобильной дороги определяется, в основном, грузовыми автомобилями, имеющими давление на ось 10 — 13 тонн, а в некоторых случаях и выше. Несмотря на принимаемые меры, в последние годы наблюдается рост протяженности участков дорог с колейностью. До последнего времени в России оценка способности асфальтобетона сопротивляться развитию в нем пластических деформаций оценивалась по ГОСТ 12801. Однако такие режимы испытаний, а также применяемое при этом оборудование, не соответствуют фактической работе асфальтобетона в покрытии, при которой он подвергается многократному воздействию колесных нагрузок, значительно меньших по сравнению с разрушающей. Методы испытания колесной нагрузкой положительно зарекомендовали себя во многих странах мира, а в странах ЕС входят в процедуру проектирования асфальтобетона. При этом используется оборудование, не имевшее до последнего времени отечественных аналогов. Разработка новых методов оценки сдвигоустойчивости асфальтобетона в нашей стране сдерживалась отсутствием отечественного оборудования, позволяющего моделировать в лабораторных условиях процессы, происходящие в реальных условиях, начиная с приготовления смеси, способа ее уплотнения, а также механического воздействия на дорожное покрытие колесной нагрузкой.
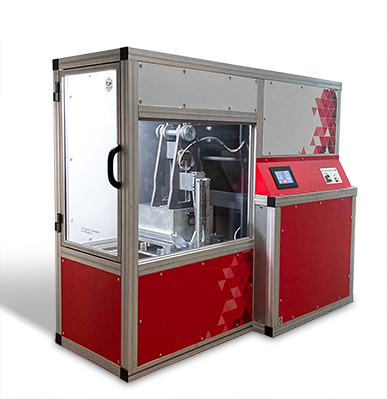
Для подготовки и формования асфальтобетонных образцов в лабораторных условиях в соответствии с ГОСТ 58406.4-2020, предприятием разработан пресс секторный ПС-30 с максимальным развивающим усилием в 30 кН (3 тонны). Пресс моделирует в лаборатории реальные условия уплотнения асфальтобетонной смеси дорожным катком. Уплотнение образца осуществляется гладким вальцовым сектором (вальцом) в металлических формах 305х305 мм. Полученные образцы затем используются для испытаний качественных характеристик асфальтобетонной смеси по системе Суперпейв:
- образцы-плиты - на устойчивость к колееобразованию по ГОСТ Р 58406.3-2020 на установках УК-2;
- вырезанные из плит образцы-балочки (призмы) - на усталостную прочность при многократном изгибе 4-х точечным методом по ГОСТ Р 58401.11-2019;
- выбуренные керны - на статическую и динамическую ползучесть, растяжение при расколе и пр.
Режим работы полностью автоматический. Параметры уплотнения задаются со встроенного блока управления.
Выбор режимов уплотнения:
- по заданной программе (величине нагружения и числу проходов вальца);
- до заданной высоты образца.
Установка УК-2 предназначена для испытания образцов асфальтобетона на колееобразование по ГОСТ Р 58406.3-2020. На установке имитируется процесс деформации дорожных покрытий под действием многократных колесных нагрузок транспортных средств. Испытания проводятся в автоматическом режиме с индикацией и запоминанием как промежуточных параметров (количество циклов воздействия, глубина колеи, температура испытаний), так и их окончательных результатов. Установка имеет климатическую камеру с системой автоматического задания и поддержания требуемой температуры в течение всего времени испытаний. По результатам проведенных на установке испытаний можно определять показатели сдвигоустойчивости образцов асфальтобетона, что позволяет, уже на этапе проектирования, подбирать оптимальные составы смесей с целью увеличения срока их службы в реальных условиях.
Главные преимущества установки:
- проведение испытаний в автоматизированном режиме;
- цифровая индикация всех требуемых параметров процесса;
- возможность подключения к персональному компьютеру;
- полное соответствие требованиям отечественной нормативной базы.
Установка может представлять интерес для проектных организаций, исследующих составы дорожных покрытий, с возможностью расчетного нормирования значений нагрузок и температур, допустимой глубины колеи пластичности на вновь строящихся и действующих автомобильных дорогах.